Today’s 3D printing applications have come a long way since the first technology pioneers explored ways to merge creativity with machine construction. Among those early wayfinders that brought us to where we are today was Johannes F. Gottwald.
What did he invent and how did his work influence today’s additive 3D fabrication technologies? In this article, we’ll explore Gottwald’s contribution to the modern world of 3D design and fabrication.
Johannes Gottwald invented tools to empower creativity
Toolmaking is a hallmark of human nature. People have always sought ways to manipulate their environment and the materials in it to create useful tools and devices.
Humans are always looking for better, easier ways to do things and early designers and inventors sought ways to automate tasks and replicate items giving birth to early sewing machines, printing presses, production lines, and the wheel.
In the 20th century, advances in electronics and computing presented a new set of opportunities to innovate. Artists and inventors used a new digital set of tools to come up with more ways to build and create.
One of those inventors was Johannes F. Gottwald.
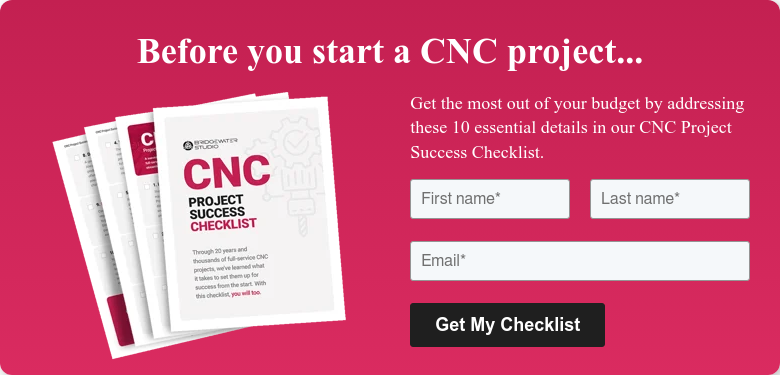
What was Johannes F. Gottwald’s contribution to 20th-century fabrication innovation?
Gottwald was working for a company called Teletype in 1969 when he applied for a patent for a machine he called a liquid metal recorder. The patent was granted in 1971 and later assigned to the AT&T Teletype Corporation.
Text of the technology claimed by Gottwald in the 1969 U.S. patent application filed by Teletype Corp.
The liquid metal recorder modified inkjet printing technology (which was relatively new at the time) to use liquid metal as the medium. To print, the device had to warm metals with a low melting point until they were liquid, then transfer the metal onto a carrier—shaping it into the desired form—where it would cool before being removed.
It was probably a little like drawing with a hot glue gun or soldering iron.
While the idea was sound, the inventor noted in his patent that the materials necessary to create large displays using the technology were limiting factors. After all, who wants to keep a stash of metal in their office to facilitate printing?
What makes Gottwald’s invention such a big deal?
Gottwald wasn’t the only tinker to imagine ways to create the items we envisioned using machines to manipulate materials. Other creative thinkers before and after him, including Joseph E. Blanther, Murray Leinster, and Hideo Kodama, would dream of ways to build using tiny particles that could be placed using simple machines, electric-powered tools, and eventually digitally-driven devices.
It may seem obvious now, but at that time, making the leap from ink on paper to metal on metal was a significant step. Gottwald’s patent pointed the way for other inventors who shared his idea that a machine could enable builders to use additive production methods at scale. Eventually, Bill Masters’ stereolithography (SLA) printing process and Chuck Hull’s 3D printing device would pave the way to bring 3D printing to the masses (or at least to the makers).
By the way, the term 3D printing refers to a method of construction, not the end results. Both 3D printing and CNC machining are modern techniques used to create 3-dimensional objects. 3D printing refers to the making of those objects using additive methods like a bird adding twigs to build a nest. CNC fabrication is subtractive, carving away from a solid material to make a shape–like an animal digging out dirt to make a burrow.
Their creative drive led yesterday’s inventors to pursue ways to expand the use of materials for additive fabrication at scale.
The journey from liquid metal to today’s 3D printing technology
Thanks to the efforts of 20th-century inventors, many manufacturers, designers, artists, and inventors keep stashes of metal, plastics, and other materials on hand to feed the 3D fabrication devices of today.
Here at Bridgewater Studio, 3D scanning, printing, and sculpting technologies combined with our CNC capabilities enable us to create highly detailed, lightweight pieces in a variety of materials to fulfill our clients’ dreams of creating immersive brand experiences. These 3D elements bring depth and architectural details to experiential marketing displays, museum exhibits, product demos, trade show booths, pop-up activations and all the other immersive experiences our customers can imagine.
Learn how full-service design and fabrication companies use today’s 3D printing and fabrication technologies to transform your ideas into remarkable experiences by booking a free strategy session with Bridgewater today. We'll help you match the right technology with your budget, timeline, and objectives and handle it all with a single partner and single point of contact for your entire project.